The manufacturing supply chain controls the flow and coordination of goods provided through a company. In short, it takes raw materials and turns them into products that create net value. SCM builds a competitive infrastructure and synchronizes supply with demand through materials, demand for those materials, and resource capacity.
The supply chain in manufacturing is a complex process that involves various stages, from sourcing raw materials to delivering the final product to customers. A manufacturing company must carefully manage its supply chain manufacturing process to ensure efficiency and quality.
By optimizing the supply chain of a manufacturing company in English, businesses can reduce costs, improve lead times, and enhance customer satisfaction. It is essential for companies to streamline their supply chain manufacturing to remain competitive in today’s global market.
Each company has constraints, so SCM increases its cash flow by synchronizing its inner processes despite those constraints. That cash flow gets managed through item flow (throughput, if you want to get technical), inventory, and expense to maximize optimization. Ideal SCM achieves data-driven customer devotion and operational flexibility.
Importance of Supply Chain Management in Manufacturing Industry
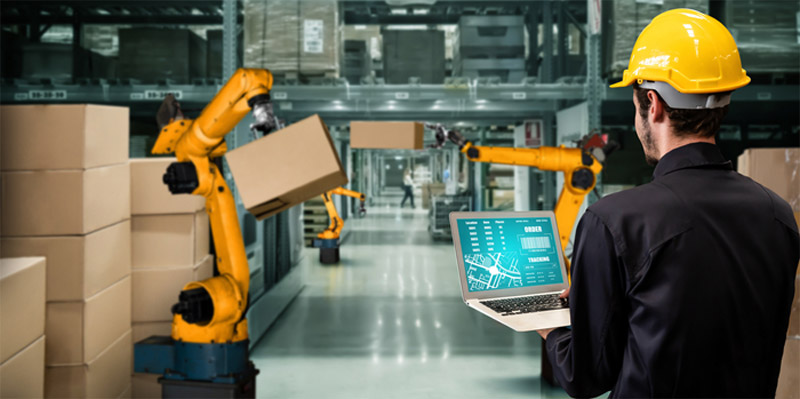
In many ways, supply chain management coordinates every process within a company, such as raw materials, resources, and workers.
SCM plays a considerable role in the manufacturing industry in coordinating raw materials and resources, accomplishing the primary goal of producing a high-quality product.
How well-coordinated a company’s SCM is can impact customer satisfaction and how much the company spends to make its products.
Technology is also playing a more prominent role in production, so SCM must take a lot more care to keep things running smoothly. In a nutshell, SCM is all about manufacturing efficiency, preventing waste, so companies don’t overspend on raw materials.
The Role of Manufacturing Supply Chain Management
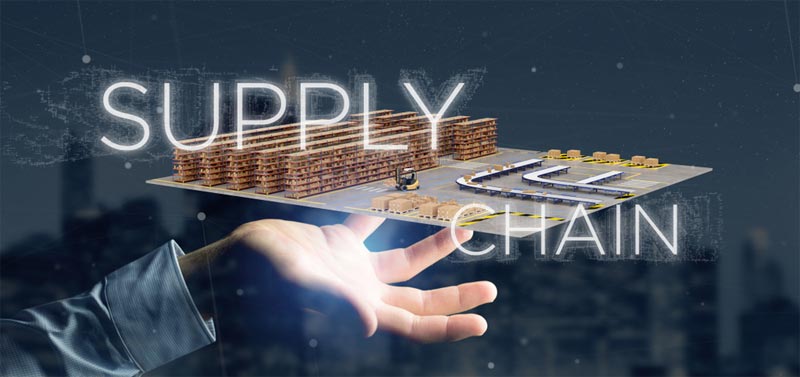
Manufacturing has evolved from a production orientation to a customer orientation. It is now critical that companies establish trading partners as valued customers with whom they share business processes and information, particularly their manufacturing orders, production plans, and forecasts.
Manufacturing supply chain management (MSCM) is not a set of discrete business functions. It is an integrated capability that defines the relationships among these functions to help a company’s product design, source, make and deliver products to their customers cost-effectively time.
Impacts of the Manufacturing Supply Chain in the Global Economy
A critical element of the world economy is the manufacturing supply chain, and it is used by most countries. In addition, the manufacturing supply chain enhances an organization’s competitiveness since it enables it to create new products. Their order processing systems and production systems must be efficient in order to meet product demands in the global marketplace.
An economy’s manufacturing supply chain affects its output and input pricing according to COVID 19. Input pricing for this would be raw materials and parts needed to create an end product. Pricing for output would be affected by chain efficiency.
Manufacturing Supply Chain Process Flow
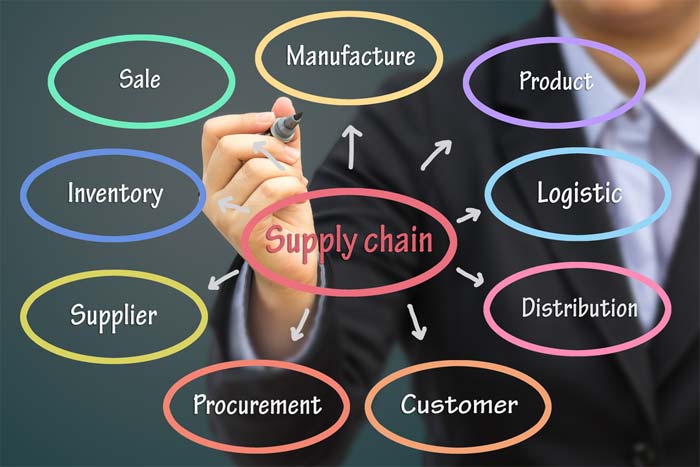
We can imagine manufacturing and supply chain as the assembly of an apple pie. An apple pie is a product that will eventually reach consumers but gets assembled from different parts.
You need to coordinate where all the required materials for assembly come from since they don’t come from the same supplier. For a pie, you’ll need different elements to make the crust, the filling, and the tin that the pie will go in.
Concepts & Principles of Product Supply Chain
There are seven principles and concepts that supply chain analysts and manufacturers abide by to condense the most important parts of manufacturing and supply chain.
1. Adapt supply chain based on each customer’s needs.
2. Customize logistics networks when needed.
3. Align demand planning across every stage of production.
4. Customize product after customer orders it.
5. Outsource to subcontractors strategically.
6. Develop IT teams that practice multi-level decision making.
7. Use both service and financial metrics.
Manufacturing Supply Chains and Sustainability
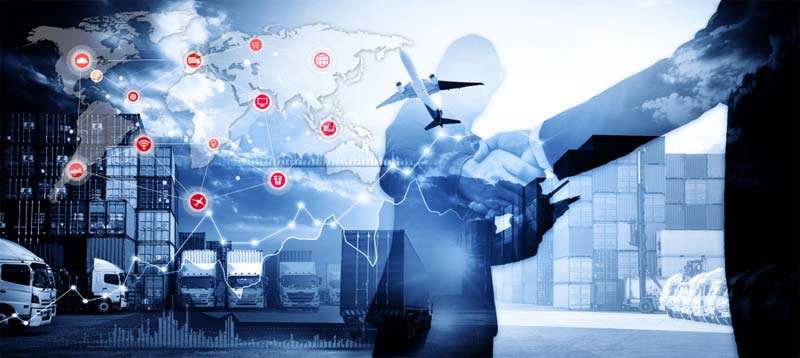
Manufacturing supply chains (MSCs) can be viewed as a system-of-systems (SoS) in which the subsystems, such as production facilities and logistics networks, are open and interact with each other. Challenges arise from interactions among multiple resources at different levels of functional granularity within an MSC. These challenges make it hard to understand, design, and manage the MSC in a sustainable way.
A key challenge is how to sustainably allocate resources among subsystems while maintaining network connectivity under multiple resource constraints such as energy consumption and production demands. This paper proposes a new SoS-oriented approach for studying and managing the sustainability of manufacturing supply chains at multiple levels of granularity.
The importance of forwarding vertical integration in Business
It is a crucial component of any business strategy to have forward vertical integration. The forward vertical integration of supply chains is when a company controls some aspect of the production process, instead of merely buying finished products on the retail market. In this case, the company may provide its distributors as well as independent distributors. Forward vertical integration can help avoid middlemen costs by allowing the original producer to keep more profit for themselves.
Manufacturing Supply Chain Examples
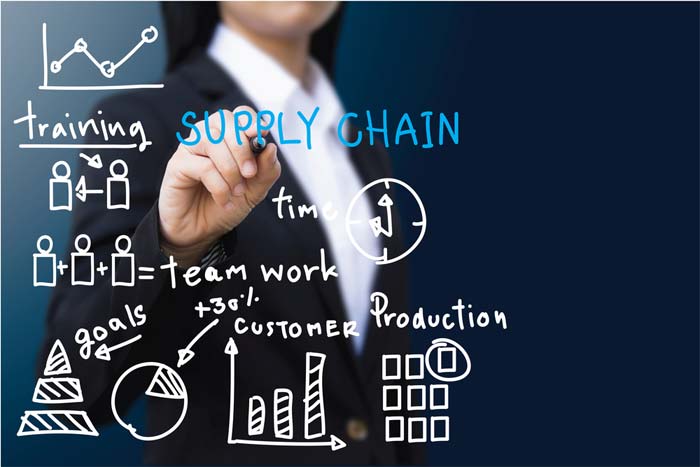
Walgreens is one real-life example of a manufacturing supply chain. They operate one of the largest pharmacy chains in the United States, so they need to constantly revise their supply chain to keep up with trends and pharmaceutical demand.
In 2016, Walgreens created SCM that uses relevant data to predict customer purchases to meet expected demand. That is, they anticipate how severe the upcoming flu season may be, so they can predict how much over-the-counter flu medicine people may purchase.
Such predictions are essential, so they don’t order too much medicine that might go to waste. Warehousing and transporting all that medicine costs money, so SCM helps Walgreens not spend too much money on warehousing and transporting medicine they won’t need.
Company Infrastructure
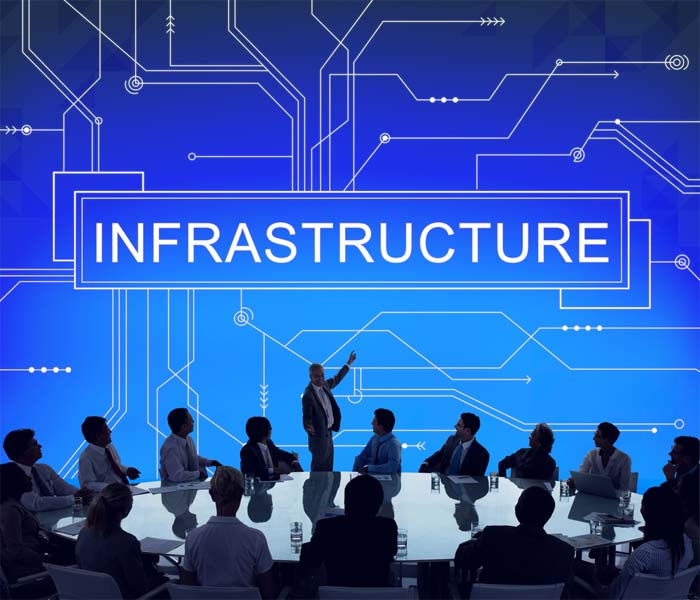
In SCM, company infrastructure refers to how a company organizes itself to achieve a set goal. Infrastructure includes equipment and technology, the staff, and maybe even whether contract employees are required.
A company can plan out these infrastructures in many different ways, as long as they do so in a way that reaps the most benefits. One company might choose to invest a lot of time and money in a manufacturing contractor.
However, another company might spend more money on equipment, so they have more control over their processes, particularly distribution.
Additive Manufacturing
Another term for “3-D printing,” additive manufacturing is becoming essentially prominent in the manufacturing and supply chain world. It increases companies’ manufacturing capabilities by simplifying manufacturing processes.
Additive manufacturing allows the local production of different parts. Many parts can also get produced at once. You don’t need to procure multiple pieces to make a single product: those parts get produced at once, without the need for shipping multiple parts and risking delays and bottlenecks in production.
Small manufacturers can take parts from a digital inventory and quickly print them anywhere in the desired quantity. This helps to cut costs by a great deal in terms of no longer having to perform physical inventories. In short, additive manufacturing has helped to transform manufacturing processes for better productivity.
Planning for Production
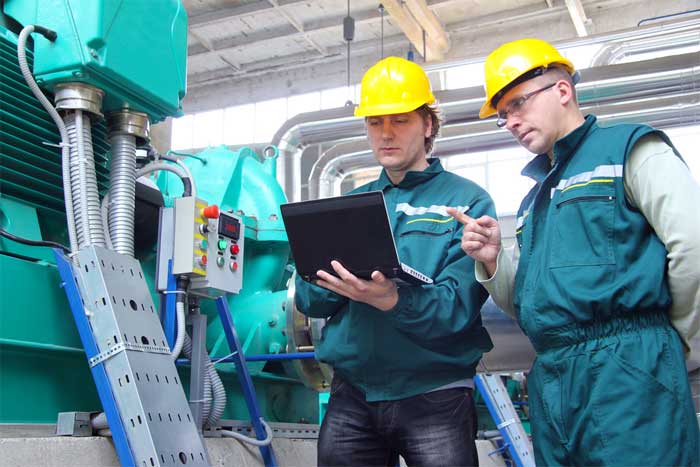
While the manufacturing operations and supply chain are chaotic, there is an order to all production processes, no matter the service or product. Strategic planning evaluation and optimization of the whole SCM process start here.
Companies decide upon locations, transportation, products, and resources to prepare to reach out for what they need. Vendor analysis, purchasing stats, and supplier performance help evaluate potential suppliers for required materials.
Demand Planning
Anticipating demand for supplies is a big part of SCM. Analysts predict future demand for a product based on statistical methods and causal analysis or just plain human judgment.
Lifecycle planning also happens during this process. That is, analysts predict the launch, maturity, and eventual discontinuation periods of different products. Promotional planning, or essential marketing, involves planning special events separate from the product’s general forecasting.
Promotions are forecasted using past promotional impacts and how they can get projected into future product promotions. Manufacturers can take competitive advantage of special holidays, contests, quarterly advertising campaigns, etc., to maximize their promotional impact.
Supply Planning
Now it’s time to order the supplies to make the number of products predicted to sell. Manufacturing facilities get outsourced to third-party subcontractors, and short-term strategies for allocating supplies to meet customer demand and replenishing stocking locations get figured out.
The manufacturer also collaborates with the supplier to receive the demand and stock information, performing replenishment planning tasks.
Supply Chain Models
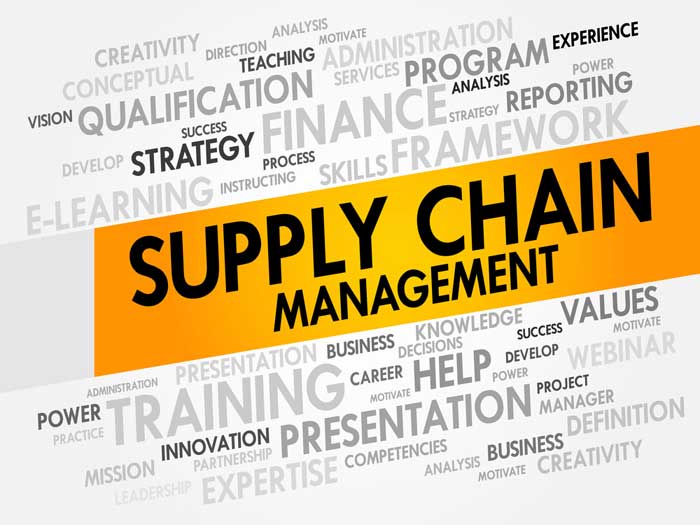
The supply chain is the backbone of every successful business. A supply chain model allocates resources and manages inventory to maximize efficiency for a company.
Whether you are looking to build a new manufacturing facility or you are trying to determine how much inventory your company is going to need next month, these models can help you.
The grid supply model determines the necessary quantities of each product that must be delivered at every time interval throughout the planning horizon.
The solution is supplied in two parts: (1) the spreadsheet that solves for the optimal parameters given your input data, and (2) a more detailed explanation of the steps taken to solve for these optimal parameters. The spreadsheet provides an estimate of the total cost at each node in the network starting with allocating resources.
Procurement Process
Procurement is where all departments get word that ordered goods are received and confirmed. Any invoices are checked for correct information before they are received and entered in.
Manufacturing and Warehousing
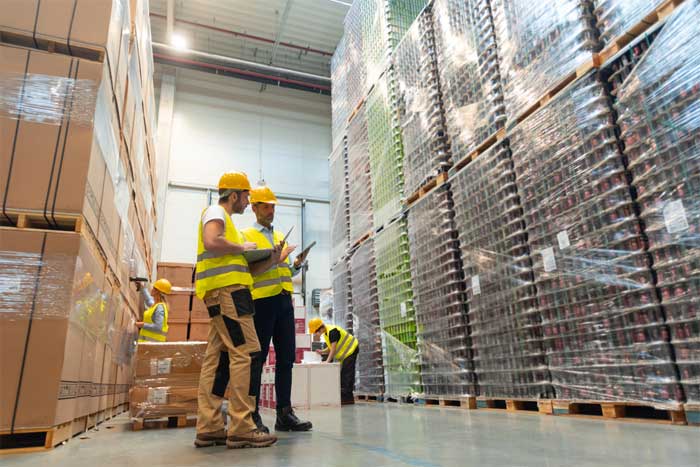
Production orders now get assigned with time frames and production sequences. Different departments receive the finished goods and prepare to ship them to their destinations, while distribution centers or warehouses keep track of where various products are stored.
Order Fulfillment
Orders for where products are shipped get scheduled for delivery. Invoices are written and received for stock locations.
Transportation
An optimized transportation plan for all products gets drawn up. Shipments get monitored, and freight costs get calculated and settled. How Is Supply Chain Management Different for the Manufacturing Industry? Supply chain management usually gets divided between manufacturing and service firms.
SCM is vital to the manufacturing industry because of how much coordination it takes to predict, procure, and ship different parts. If shipments get delayed or bottlenecked, problems can arise. It requires a lot of focus on physical products and a broad supplier base.
The service firm supply chain is different in that it doesn’t need as many physical inputs. They also work with small manufacturers. They don’t require as much capital investment in machinery and equipment. How Does Contract Manufacturing Make the Supply Chain More Efficient? The supply chain involves many moving parts.
As a result, many companies choose to streamline their supply chain management. Partnering with a knowledgeable company about contract manufacturing models might save you time and money in designing your company’s infrastructure. Some benefits of contract manufacturing making the supply chain more efficient can include the following:
Improved Productivity
As mentioned before, contract manufacturers help streamline supply chain procedures to make the manufacturing process go more smoothly. They can help with issues like helping merchandise not be late, finding the best-working equipment or machine parts, and finding the company’s best staff.
Reduced Mistakes
Contract manufacturers are good at helping with multiple supply chain management stages, allowing the company to reduce mistakes. They can also double-check that each stage of production is flowing smoothly.
Raised Profits
When trying to raise profits, some companies cut corners. The reality is that you can better boost profits by simply eliminating mistakes. Contract manufacturers, as mentioned, can help reduce the number of errors and help you save, or merely make, more money.
Since contract manufacturers streamline the supply chain, orders can get completed sooner, which reduces fatigue for employees, therefore saving on downtime.
Save cost
The most immediate benefit you’ll notice when working with a contract manufacturer is the lower cost. Lower costs at every stage of production lead to higher profits. Lower costs also mean less waste and fewer resources, which can provide an environmental benefit.
Contract manufacturers know how to work efficiently, so there’s no need for wasteful practices that ultimately just increase your expenses. A company’s financial standing is improved when costs are low.
Consultation on SCM Strategy
Partnering with a contract manufacturer can give you a lot of insight into the production process. They have some kind of responsibility in each step of manufacturing, which means they have a good idea about SCM strategy, and you’ll spend less time wondering what the SCM issue might be.
Better Communication
Some companies might try to communicate with several manufacturers or people to create just one product. Having only one leading SCM partner cuts down on the explaining or general communicating you must do to get the job done.
You might find specific issues along the way, and they get fixed faster when you only have to communicate to one company about it. When talking about different processes or procedures, it’s easier to only relay that information between your company and the manufacturer, saving time in the long run.
Improving communication is especially important since many suppliers are involved with creating one product, and miscommunications can occur among parties. Therefore, try keeping communication with only one contract manufacturer.
Improved Reputation in the Industry
Many companies see partnering with a contract manufacturer as an opportunity for more business. The reason they do this is that there are fewer risks involved when you partner with people who’ve already worked together, know the industry well, and produce quality products.
If they haven’t seen someone’s work before, there’s more of a chance for mistakes than if the company has already done work with them. There’s also a good chance you might see your business expand if the manufacturer likes working with your company and thinks it can help provide opportunities to others, too.